Performance Diesel 101 – Gale Banks Engine Balancing
Balancing an engine allows it to run smoother, get better mileage, and last longer. But how is it done? The experts at Banks Balancing Service (BBS) took a moment out of their busy schedule to show us the procedure and answer our questions.
By John Stewart
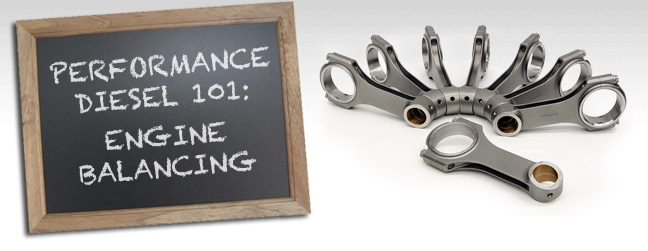
No one in their right mind would put new tires on their car without first balancing them. Unbalanced, the tires will create vibration, squirm away tread on the road and wear out quickly. It only takes a little more time to balance them properly, so they roll smoothly and last as long as possible. That’s why it’s standard procedure.
The same can be said of practically any rotating assembly. Anything that spins will start to shake and bounce around if it’s unevenly weighted. So what about your engine? Same deal. That’s especially true if it’s a diesel, which needs all the help it can get to run smoothly.
By balancing an engine, we are looking at the relative weights of rotating and reciprocating parts, making sure that the weights of pistons, rods and crank counterweights are all as closely matched as possible. It’s the kind of thing you’d want to do any time you assemble an engine. While it’s possible to fit together new engine internals right out of the box, you’d be crazy not to think about balancing the parts first.
BBS technicians balance crankshafts by attaching bob weights to the crank journals and spinning the crank on a balancing machine. The computer screen shows the source of whatever vibrations have been detected.
Piston and rod assemblies that are out of balance exert uneven forces on the crank, and a crank that has unevenly balanced counterweights will tend to flex more at higher speeds. In both cases, the result is early and irregular wear on bearings, and even if damage does not occur rapidly, the engine will have to work harder to overcome friction. There is more heat generated, more fuel burned, and long term, greater wear as internal parts chatter.
These days, more components are being made from high-strength, lighter metals, so small differences in their relative weights become more important. A single rod or piston that is a few grams heavier than average, or a few grams lighter, can make a big difference. As rpm increase, the effect of a few grams off-center increases exponentially, adding up to pounds very quickly.
Balancing a high performance engine is so critical that racers and hot rodders have been doing it for decades. At Gale Banks Engineering we do so much of it we have our own subsidiary, Banks Balancing Service, to make sure every engine we assemble is properly balanced, and to service the needs of outside customers. More on that in a minute.
To add weight to a crank, holes are drilled out in the counterweights and filled with dense Mallory metal.
Cranks, Rods and Pistons
Piston and rod balancing is about matching the weights of the pistons, and the rods, so they all weigh the same, or at minimum within 1 gram of each other. Pistons are usually weighed as a complete assembly, with rings and locks in place. When weighing rods, the big end and small end are weighed separately. That’s because the big end is considered rotating weight, and the small end is reciprocating weight. Once they have all been weighed, small amounts of material can be cut away until they all match the weight of the lightest rod. Once the rod ends and pistons are all equal, the crank can be balanced.
The crank is balanced by attaching weights to the crank journals, called bob weights, that simulate the weight of the rods and pistons. Bob weights are calculated, typically, by adding 100 percent of the rotating weight and 50 percent of the reciprocating weight. The crank is then spun on the balancing machine. The machine only needs to spin at about 500 rpm to detect an out-of-balance condition, after which any counterweight that is lighter than the others is indicated on the computer screen. Weight is then added or removed until all the crank counterweights are equivalent.
Most often, weight is added by drilling out holes in the counterweight and inserting appropriately-sized slugs of a very heavy tungsten alloy called Mallory, although there are some engine builders that balance a crank by removing material.
Mallory metal is a tungsten alloy that is considerably heavier than steel. Slugs are inserted to allow the weight of the counterweight to be increased without changing its shape or size.
To balance rods, each end is weighed separately. The big end is considered rotating weight, while the little end is reciprocating weight, as are pistons.
Turbo Balancing
Since they rotate at VERY high rpm, turbos also need to be strictly in balance to live a productive lifetime on an engine. Any kind of housing contact will definitely create an imbalance. Disassembly of the matched pair (or the introduction of another “partner” part) is usually the source of problem, unless there has been actual contact with the blades on either side. Service to a wheel (i.e. repairing or replacing a fin, repairing a piston ring gap or resizing the turbine shaft) will immediately cause it to become imbalanced, so especially when the turbo is rebuilt or serviced, it should be rebalanced. Symptoms of an out-of-balance turbo assembly include noise and early seal failure.
Here at Banks, we usually balance the compressor and turbine wheels by themselves, then as an assembly to ensure a perfect balance. A turbo balancing machine is used to spin the assembly and indicate the relative weights of the components. By removing small amounts of material on the wheel(s) and/or compressor nut, the assembly is brought into perfect balance. That done, the turbo should operate with lower noise and live a longer life.
Turbos are balanced by spinning the shaft, with both turbine and compressor wheels attached. The machine detects vibrations and indicates their source, so that small amounts of material can be removed to equalize balance.
Banks Balancing Service
Since 1953, Banks Balancing Service, formerly Automotive Balancing Service (ABS) has been the go-to balancing operation for racing’s brightest stars and their most groundbreaking achievements.
Founded by Bill Fisher as Electronic Balancing Company in 1953, the firm originally took on industrial applications (fans for refrigeration, air conditioning and industrial machines) as well as automotive and aircraft engine-balancing applications. Cecil Welch, Fisher’s childhood friend, joined the firm shortly thereafter. As the workload increased, Fisher turned over all of the automotive work to Welch, who set up shop in Lynwood at 11019 Atlantic Avenue. It was 1956, and Banks Balancing Service-the very first high-performance engine balancing shop-was born.
Gale Banks’ association with BBS goes back to 1958, when Banks owned a nearby speed shop in Lynwood. Gale chose BBS to ensure precision balancing of his high-performance auto and marine engines. After that, BBS balanced the Banks engines for many of Gale’s record-breaking speed runs at Bonneville, including World’s Fastest Passenger Car (268 mph in 1986), the World’s Fastest Piston-engine Automobile with Al Teague (432 mph in 1997) and the World’s Fastest Pickup Truck, the Banks Sidewinder® Dakota (222 mph in 2002).
BBS’ capabilities include custom connecting rod service, Magnaflux inspection of crankshafts, rods, pistons, axles, spindles, etc. BBS also provides expert piston matching, crank polishing, crossdrilling, keycutting and other specialized machining services.
Visit the Banks Balancing Service website »