P3= Printing Pliable Parts
Banks Engineers are working hard to use every bit of available space in the engine bay to develop the 2010-2012 RAM intercooler. The new intercooler tanks and core are being designed with the unequaled flow, but sometimes taking advantage of the available room means that the inlet and outlet of the end tanks won’t fit with the boost tube’s pathways. That’s when the Banks engineers have to get tricky with how things connect, making sure that there are no compromises in airflow in order to fit into the tight confines under the hood.
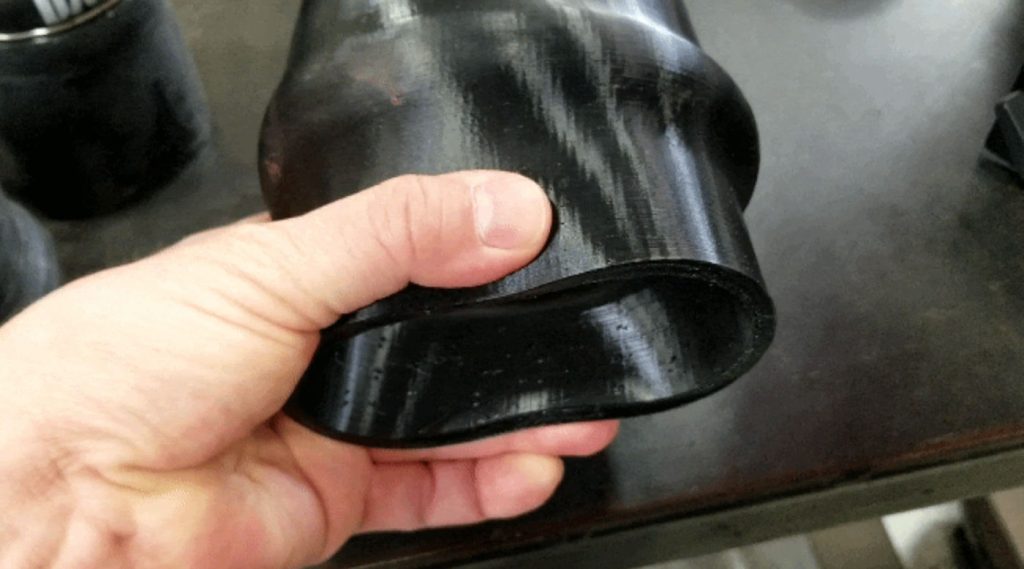
In order to join this new design to the boost tubes, new couplers are also being designed. These prototypes are being printed with TPU or Thermoplastic Polyurethane. This is the same material used commonly for things like shoe soles, phone cases, golf discs, etc. With the right equipment, it can be used in filament form for 3d printing, which allows you to print flexible, rubbery parts. The print will not be able to handle the pressure of the charge air so the parts are not useable on the truck to run, but work great for prototyping as they are flexible enough to be pushed over a hose bead and clamped in place just like a real silicone hose.
The Intercooler for the 2010-12 RAM 6.7L is scheduled for release later this year.