Diesel Land Speed Record — Goal of Project Sidewinder
Diesel Progress August 2002
210+ mph in Dodge Dakota … illustrating diesel as a performance engine … 600 hp out of 5.9L
With an eye on a new diesel land speed record, Gale Banks Engineering has developed the Cummins-powered project Sidewinder Dodge Dakota. The attempt at the record will be during Bonneville Speed Week this August, as well as the Bonneville World Finals. The goal of the program is to establish new speed records in excess of 210 mph using a compression ignition, turbocharged engine powering a street driven and tractable Dodge Dakota pickup.
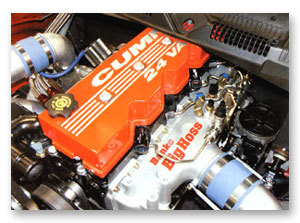
Power for Project Sidewinder is a Cummins 5.9 L, 24-valve, in-line, six-cylinder base-line engine utilizing a Holset HX40 turbo. Displacement is 359.0 cu.in. with a compression ratio of 15.1:1. Power output is 393 bhp at 3800 rpm and 600 lb.ft. of torque. The electronics are from Cummins.
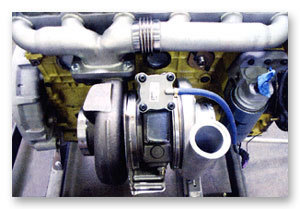
Project Sidewinder uses Holset variable geometry turbochargers. A modified HY55 turbo will be used for Bonneville speed record runs, while a smaller HY40 unit will be fitted for street use.
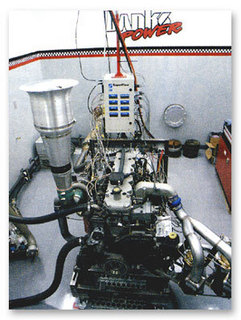
To test the engine, Banks installed a compression ignition engine dyno that is able to handle up to 1000 hp, 3000 lb.ft. of torque and engine speeds of 5000 rpm. This configuration allows testing of components and systems for the Sidewinder Project and future high-speed compression ignition engine development. The dyno is based on a Superflow dyno model SF3100, a Superflow Pro-console with Windyn software.
A new high profile engine and vehicle development program has its sights set on a new diesel land speed record at Bonneville Speed Week this August, as well as the Bonneville World Finals. The program, called Project Sidewinder, brings together Cummins Inc., Gale Banks Engineering, along with Holset Turbocharging, New Venture Gear, the Progress Group and Wilwood Engineering.
The goal of the program is to establish new speed records in excess of 210 mph using a compression ignition, turbocharged engine powering a street-driven and tractable Dodge Dakota pickup.
The current diesel pickup truck record in the Sidewinder’s class is 153 mph. The fastest ever pickup on the salt was Gale Banks Syclone GMC pickup at 204 mph in 1989. The target speed for the Sidewinder is over 210 mph.
If that wasn’t enough, street legal drag races, both quarter and eighth mile events, are on tap for the Project Sidewinder Dakota. The goal is to establish strong elapsed times and speed records for a diesel-powered sport truck. Further, magazine road test exercises, including zero to 60 mph acceleration, 60 to zero mph braking, 200 ft. diameter skid pad and the 700 ft. slaloms will be undertaken to demonstrate the street performance of the Sidewinder Dakota.
“We want to drive the Sidewinder to the Bonneville Speed Trials, towing our racing gear, with great fuel economy,” said Gale Banks, President of the Azusa, Calif., company that bears his name. “Then we want to put on the proper wheels and tires and go racing. And we want to eclipse the current National Speed Record.
“Diesel has a negative image in many quarters. We intend to erase that image. The whole idea of the Sidewinder Project is to illustrate that a diesel can be an extraordinary performance engine. There are a lot of people that if they were considering a light truck or sport-ute, wouldn’t even consider diesel.
“If we can illustrate through the Sidewinder that you can have a high performance street vehicle that is diesel powered, then I think we’re going to break down a wall with all those potential buyers, nationwide,” Banks said. Banks also said he will use the Sidewinder to commute to work.
The Banks Race Shop in Azusa prepared the Dodge Dakota pickup and included all the creature comforts for highway driving. Banks installed a compression ignition engine dyno that is able to handle up to 1000 hp, 3000 lb.ft. of torque and engine speeds of 5000 rpm. This configuration allows testing of components and systems for the Sidewinder Project and future high-speed compression ignition engine development. The dyno is based on a Superflow dyno model SF3100, a Superflow Pro-console with Windyn software.
Power for the Sidewinder Project is a Cummins 2003 in-line six-cylinder compression ignition engine with common rail injection that develops 600 bhp and 1000 lb.ft. of torque. The engine is fitted with a Holset variable geometry turbocharger. The driveline includes a New Venture six-speed gear-box, Wilwood braking system, Progress Group coil-over-spring/shock units.
Banks’ Rich Shahoian said the Dodge Dakota platform provides a smaller, lower-drag aerodynamic package for top speed runs. With less frontal area and a slightly smaller coefficient of drag, the Dakota requires less power to reach 210 mph than the larger Dodge Ram package. Since the Project Sidewinder is a street vehicle, Shahoian said power goals must take into account the tract-ability, efficiency and reliability needed on the highway.
In order to determine the power needed to reach the speed goal of 210 mph at Bonneville, the power at the rear wheels, top speed and aerodynamic and parasitic drag must be determined for the stock truck. Initial chassis dyno testing was needed to determine horsepower and torque at the rear wheels for the stock truck.
The Banks team was able to calculate the amount of horsepower required to reach 210 mph. Well over 800 hp would be required with the Dakota in stock trim at stock ride height.
Since the Cummins Turbo Diesel engine in race trim is projected to produce 600 hp (on straight diesel fuel), considerable drag reduction was needed to reach the desired speed of 210 mph at Bonneville. Lowering the truck will reduce frontal area and an air dam and other allowable aerodynamic, modifications will reduce the drag coefficient.
The engineering team at Cummins built the base engine, code named, “Salt Quake” for the Sidewinder Project. This is the same basic engine that Banks will further modify for Bonneville. This engine will be used in baseline testing in preparation for the myriad motor sports activities for Project Sidewinder.
The Cummins baseline engine is a 5.9 L, 24-valve, in-line, six-cylinder design utilizing a Holset HX40 turbo. Displacement is 359 cu.in. with a compression ratio of 15.1:1. Power output is 393 bhp at 3800 rpm and 600 lb.ft. of torque. The electronics are from Cummins.
Porting and polishing on the four-valve-per-cylinder head as flow tested in preparation for dyno testing. Optimum intake and exhaust valve sizes are also being determined in an effort to extract maximum flow from the heads.
Two different intercooling systems are required for the vehicle. On the street, drag strip and road racing venues, an air-to-air intercooler will be used to reduce the temperature of the boosted air. At Bonneville, the length of the run will require a water-to-air intercooler with a large tank mounted in the bed of the truck to hold cold water. The weight of the water tank will also serve as ballast for the high-speed runs.
Project Sidewinder will use Holset variable geometry turbochargers. A modified HY55 turbo will be used for Bonneville speed record runs, while a smaller HY40 unit will be fitted for street use.
The electronic controls for boost and fuel delivery are in-house engineering projects of Banks engineers. Boost control is crucial for optimum performance. The common rail fuel injection, operating under extremely high fuel pressure, requires electronic control of solenoids which inject fuel directly into each cylinder. The fuel injection system uses an inlet metered high-pressure fuel pump with eccentric cam pump, and three pumping elements. The fuel flow requirements for 600 hp will approach 200 cu. mm/stroke.
The engine was matched to a New Venture NV5600 transmission, a six-speed, manual shift model found in 4×2 Dodge Rams with either V10 or the Cummins 5.9 Turbo Diesel. Complete blueprinting was undertaken by the New Venture technicians assuring that the transmission shifts smoothly and provides the highest level of reliability. Otherwise the gearbox is completely stock with the following gear ratios: first – 5.63; second – 3.38; third – 2.04; fourth – 1.39; fifth – 1.00; and sixth – 0.73.
A massive clutch system was needed to control the 600-plus hp produced by the engine. The clamping force required to harness the torque output demanded a custom built 12 in. dual disc system with a precision ground billet steel fly-wheel. The material used on the disks is an organic compound with a Kevlar weave for added strength and durability.
The clamping force produced with this assembly is in excess of 1200 lb.ft. The larger diameter of the dual disc system provides an optimum compromise between controlling the power, and allowing for easy street driving when compared to off the shelf small diameter multidisc clutch systems.