Banks Sidewinder Dragster Gets More Power
Diesel World February 2012
GM Duramax 6.6L LML engine gets SUPERCHARGED at Gale Banks Engineering
Gale Banks has always been known as a hot rodder, drag racer and automotive engineer. Over the past 45 years, he has created some unique and fast cars, trucks and dragsters that have set numerous drag racing and land speed records.
Gale was an early diesel performance pioneer, calling the diesel engine a “clean-burning way to develop high performance while creating better mileage than the conventional gasoline-powered engines.”
Banks Power, in Azusa, California, developed a GM 6.6L LMM Duramax diesel engine featuring twin turbos that produced 1,250 hp and 1,300 lb/ft of torque. The foundation of the second-generation Top Diesel engine is a GM 6.6L LML Duramax diesel.
The Bennett Racing billet crankshaft was given more mass material to the crankshaft counterweights. These were then balanced to eliminate rotating mass harmonics due to increased load-created by the increased weight of the twin Fluidamper 8-inch harmonic balancers and pulley assembly on the crankshaft.
A set of Carrillo connecting rods links the Banks-designed, Mahle-manufactured 16.5-10-1 forged aluminum pistons. The engineers at Banks designed and machined a custom aluminum intake plenum and runners for optimum airflow. A pair of Banks-developed, CNC-ported, aluminum, four-valve cylinder heads delivers the precise air and fuel mixture to guarantee maximum horsepower.
The mighty Duramax gains enhanced power for a Whipple 4L screw-type supercharger. Mike Spitzer, from Greenfield, Indiana, designed and built the Sidewinder Top Diesel Dragster. The chassis was made from 4130 chrome-moly round tubing, and the chassis was covered with a carbon-fiber body and wings.
I had the opportunity to follow along as Banks Engineer Technician Mike Keegan assembled the Banks generation-two GM 6.6L RPO LML Duramax Top Diesel Engine.
1. Walking into the Banks engine assembly room was like walking into a surgical room because of the pre-assembly of the pistons, wrist pins, connecting rods and bearings. | ![]() |
2. The rotating mass is linked with Carrillo standard connecting rods. | ![]() |
3. The combustion chamber in diesel engines is actually in the top of the piston, rather than the cylinder head, as in gasoline-powered engines. A set of custom Mahle 2618 aluminum pistons was designed and machined with a specific bowl recess, conical shape and crown reliefs to create the optimum combustion performance. | ![]() |
4. After assembling the pistons and connecting rods, Mike Keegan carefully installs the piston rings into the ring lands. | ![]() |
5. A 4.080 piston ring compression was used to keep the rings compressed in the ring lands while Mike carefully lowered the piston into the cylinder. | ![]() |
6. The connecting rods and pistons were successfully installed into the cylinders. | ![]() |
7. Dual height gauges were used to find the TDC (exact top-dead-center) of the piston travel in each of the cylinders. | ![]() |
8. With the engine block rotated on the engine stand, we can see that the Bennett Racing billet stroker crankshaft was secured with the crankshaft main caps and ARP bolts. | ![]() |
9. Notice the extra weight added to the crankshaft counterweights to dampen the rotating mass harmonics. | |
10. A set of bronze valve guides was tapped into the cylinder heads. | ![]() |
11. Next, a set of ARP head studs was threaded into the engine block. | ![]() |
12. The GM LML port and polished aluminum cylinder heads were installed onto the engine block. | ![]() |
13. Check out the custom intake plenum and pair of runners that were machined at Banks. | ![]() |
14. The intake plenum was ported and polished for optimum airflow. | ![]() |
15-16. The intake plenum and runners were then installed atop the engine block between the cylinder heads. | ![]() |
15-16. The intake plenum and runners were then installed atop the engine block between the cylinder heads. | ![]() |
17. A Banks harmonic balancer was bolted onto the crankshaft to eliminate vibration. | ![]() |
18. After the pulley system was mounted to the billet aluminum bracket, the secondary serpentine belt was routed. | ![]() |
19. Mike aligns and mounts the black Whipple 4-Liter screw-type supercharger to the plenum. | ![]() |
20-21. A nitrous oxide stage 2 system, along with water-methanol, is used for added neck-snapping power and torque. | ![]() |
20-21. A nitrous oxide stage 2 system, along with water-methanol, is used for added neck-snapping power and torque. | ![]() |
22. A pair of Banks custom 2 ½-inch-diameter stainless steel “zoomie”-style headers was bolted up to the cylinder heads. | ![]() |
23. The factory LML valve covers were tentatively mounted to the cylinder heads. They will be replaced with Banks cast aluminum valve covers. | ![]() |
24. Large Bosch injectors were used to deliver the massive amounts of fuel of demand. | ![]() |
25. A dual remote oil filter system with Wix 51515R filters maintains micro-clean oil. | ![]() |
26. A multi-dry sump oil system guarantees optimum engine lubrication. | ![]() |
27. They say a picture is worth a thousand words. Well, start counting. How about 1,500 lb/ft of torque @ 6,500 rpm and 1,500 horsepower @ 6,500 rpm! | ![]() |
28. The Mike Spitzer top fuel alcohol chassis will be home for the newly redesigned and built Banks GM DuraMax LML 6.6L Sidewinder Top Diesel engine. | ![]() |
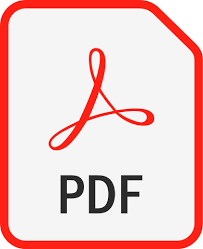
Download this article as a PDF »
Be sure to visit dieselworld.com »