Heavy Duty, High Performance
race engine May 2016
Over the years, Rudolf Diesels creation has taken a back seat in the world of race engines to traditional spark ignition motors. Consigned in the main to heavy load-lugging and industrial applications, it 151 past 30 years that the racing world has begun to wv the true potential of compression ignition for competition use, the most significant successes to date being the recent eight-year dominance of diesel engines in endurance racing, with the highly advanced products of Audi and Peugeot battling it out at the Le Mans 24 Hours. In Europe, diesel has long been a favoured fuel for roadcars, but in the US it has largely been ignored, it being rare to find a diesel engine in anything other than a pick-up truck or freighter. ln recent years, however, there has been a steady increase in interest in pushing these heavy-duty engines into competition use, with applications ranging from drag racing to powerboats.
For many years, Cummins engines were the only real option for anyone wishing to build big-horsepower diesels, but since the end of the 20th century, manufacturers such as Ford and GM have started producing a range of modern, large-Capacity units. These have paved the way for aftermarket tuners to push diesel engine power outputs to previously unheard of levels. Of these new engines, the Chevrolet Duramax, introduced in 2001, has proved a firm favourite with racers, and one such fan is long-time racer and renowned engine developer Gale Banks, who has been involved in building some of the most advanced diesel race engines unrelated to the factory efforts of the likes of Peugeot and Audi.
The Duramax was developed predominantly by Isuzu for GM, which needed an all-new diesel for its new -for- 2001 heavy-duty pick-up truck range, with Isuzu handling engine design and GM the integration into its vehicles. The standard engine was a 6.6 litre, 90° V8 with direct injection and four overhead valves per cylinder, which were pushrod operated. Banks says the Duramax became ‘the’ candidate for tuning as soon as it was launched. All the engines built up until the introduction the Duramax in 2001 had a design that was more agricultural a more in common with haulage truck engines, so they were massive components with very low speed, maybe 3200 rpm peak, he says. “The Duramax, when I first saw one that had been taken apart, looked like a Big Block Chevy inside. If you’re going to build a competitive diesel engine, the Duramax is the benchmark.
Rotating components
Banks has worked extensively on the development of parts for the Duramax system for high-performance use, and the methods applied in the process are common across Banks Powers (Banks Company) diesel tuning programmes. The foundation of any of its programmes if finding the limits of the base engine structure and then using that as a starting point for development.
The route to obtaining big power is similar to that with a spark ignition engine – the need to fit as much air and fuel into the combustion chamber on each cycle and then ensure the fuel iscombusted as completely as possible. The type of diesel engines Banks builds are not of the variety seen at truck pulls ‘rollin’ coal though; as he rightly points out, a thick black exhaust plume is just wasted fuel energy and means the engine builder is not doing their job properly. The challenge comes in persuading engines that are designed around being low-speed, high-endurance units to rev to levels where useful horsepower can start to be made.
Explaining how the capabilities of a particular engine combination are established – be it a Duramax, a Cummins or a Ford Powerstroke Banks says, “We do a lot of combustion analysis, and we are measuring cylinder pressures at every quarter of a degree of crank angle. We find the cylinder pressure limit of a particular engine design, high is sometimes quite a destructive process, although more often e find it without destruction as the cylinder head gaskets normally ran to fail, that sort of thing.
While there are some aftermarket blocks for use in drag racing a truck pulling that are stronger than the standard GM parts, in Banks’ option the lack of adequate cooling provisions rules them out for any sort of extended use.”For this reason, we try to use the stock castings, and if you respect the maximum cyclinder pressure the engine can withstand, and then hold that to a high enough rpm, you start to make a hell of a lot of horsepower. So the challenge is how to get to the higher RPM. One of the main areas of weakness Banks has found when pushing Duramax engines to higher rpm is the structural integrity of the crankshaft. “We have found that the crank in the Duramax, when you are really pushing and revving it, fails on the front crank throw, which is pretty catastrophic, “he says. He found that one of the main contributing factors to these failures was the architecture of the crank, specifically the relationship of the rod journals to the main bearing journals. Generally, the circumferences of the two journals would overlap each other, but if the stroke of the crankshaft is increased then the overlap is decreased, detrimentally reducing the amount of material at a key stress point in the crank.
Banks solution to this problem has been to completely redesign the crank and rods, with the new crank forming the basis of his latest generation of ‘big-pin’, 7 litre Duramax engines. His approach runs contrary to that of some racers, which is actually to reduce the diameter of the journals in order to be able to fit Chrysler Hemi-type (2.375 in diameter) rods. “We have developed a new crankshaft for the engine that uses a much larger rod journal, increasing the overlap between the journals. The problem then was that there was no bearing that existed at the diameter we needed, so we worked with Clevite to produce a new bearing, which was one of the toughest parts of the job, he says. Owing to the increase in the diameter of the rod journal, the con rods could no longer be passed through the bore of the engine. “To get around that problem, we canted the cap of the con rod at an angle of 40° to where it would normally be to allow us to assemble the engines, he says. “This initially gave an imbalance in clamping pressure and load on the bearing, so we had to do a lot of FEA work to check the distortion of the rod at speeds of up to 8000 rpm. But after many iterations we have come up with a viable design.” Ensuring that the new crank and rod package was durable was not simply a case of making the journals bigger and then finding a way of fitting the parts in the block. One result of increasing the bearing diameter was a related increase in bearing surface speed, so Banks had to find the right compromise between a large journal and an acceptable bearing surface speed. “If you are going to lubricate the bearings properly you simply cannot have too high a surface speed, otherwise you will start to fail bearings. I wanted to go larger with the journals than I actually went in the end, he notes.
Banks also revised the counterweight design of the crank to give better balancing. The standard Duramax counterweights are designed so that the weights are full radius but with a reduction in radius at the center of the rotation, to allow it to clear the bottom of the piston. Banks wanted the benefits of having a full-radius counterweight without this clearance, but to achieve that meant adjusting the rod and piston dimensions to prevent contact between the piston skin and the crank. I’ve extended the rods and shortened the pistons, while pushing the piston pin as high in the aluminums piston as we can, so that it actually encroaches on the ring pack, he explains.
Firing order
As well as redesigning the crankshaft, Banks has also been investigating other areas of development to help high-rpm durability with the Duramax. This has included assessing the firing order in the engine and its effect on crankshaft fatigue. He says, we have been experimenting with changing the firing order of the Duramax to that used by GM on some of its other” engines. The reason for this is that when firing a 90° VB, be it or diesel, generally you have firing impulses into the crank throws that are 90° apart on three out of the four rod journals. On the fourth one they art- M0 apart, so you can move the firing order around by moving which journal has the 270° split.”
Banks found from extensive testing that having 90° firing on the front crank throw invoked a considerable twist right at the front of the crank. “That I believe aggravates the failure mode in that front crank throw, “he says. He therefore feels that having the cylinders driving the front throw of the crank fire at 270° instead will help reduce crank torsional and increase durability at high rpm and/or cylinder pressure. “By increasing the duration between the firing impulses on the front crank throw, it gives the crank time to relax a bit, he says.
He also highlights another means of alleviating this problem beyond changing the firing order, which is to optimize the crankshaft vibration damper, which fits on the nose of the crank. “I think that a lot of guys are breaking crankshafts because the vibration dampers are not tuned to the engine combinations they are putting together, he says. “Even increasing the speed of the engine will change the calibration of the damper. If you change the crank stroke, the mass of the rod or piston assembly, then you are changing the dynamics of the crank even more. So you will need a different design of damper; it is not a case of one size fits all.”
To ensure that the dampers are matched to each engine combination, Banks Power makes its own dampers. We measure the twist of the crank while the engine is running on the dynamometer. I like to have only a +/- 0.25° of deflection on the crank front to rear, as l’ve found that when you go beyond that things start to fail,” Banks 1 says. To create a damper that matches an engine’s particular requirements, he will adjust the dampers inertial ring diameter and mass. Also by changing the viscosity of the fluid in tow damper, its damping rate can be changed. Using this approach, we can come up with a design that is incredibly durable, he says.
As a final note on dampers he says, “External counterweights, at each end of the crank, put a bending moment on the crank – big problem! At 6000 rpm, with a typical Dmax damper counterbalance weight, the bending load on the snout is 7200 lb and the crank breaks in the front throw.
Cylinder heads
With Banks new developments giving the Duramax the ability to operate at the high rpm needed to produce power, the next challenge is ensuring that the engine can ingest enough air to allow efficient combustion of the fuel. In the past, Banks has used modified standard heads for his race engines, but in recent years he has started to use an aftermarket head casting.
The choice of aftermarket heads is somewhat limited for the Duramax engine, or any other large diesel for that matter. However, Indiana-based diesel engine builder leremy Wagler, of Waller Competition Products, teamed up with head manufacturer Brodix in 2014 to produce a ranged competition heads for the Duramax, which Banks rates highly. The result is the Wagler/Banks configuration used here.
You need to find a cylinder head that can take the intake manifold air density that we produce [from the turbos] and get it into the Cylinder – that is the key to making power at high speed with a diesel. The peak mass flow of the cylinder heads is now the main limiting factor with diesel, explains Banks. To clarify the make-up of the Duramax head, there is no combustion chamber to speak of, simply a flat flick, with a piston cup forming the combustion area.
With the use of an aftermarket head, it is possible to increase the airflow of the engine considerably by enlarging the ports and valves, but Banks is at pains to point out that this cannot be at the expense of intake swirl. You have to remember that a diesel is a stratified charge engine, he says. Most of the guys who run diesel engines in the US Seems to ignore that fact or don’t know it is the case: it seems to be an attitude of I’m more masculine than you are if I put the largest plume of black smoke out of the exhaust. Basically, they are running the engines incredibly rich, which in the case of a diesel means they run hot [the opposite effect as with gasolines. To keep things cool the inject tremendous amounts of water, which is treating the symptom rather than the cause. The problem is that they are injecting too much fuel and have lost the swirl effect through the modifications they make to the cylinder heads.”
Most diesel engines have two individual intake ports feeding each intake valve. Banks refers to these pairs of ports as the swirl port and the mass flow port. “The swirl port causes rotation of the air in the cylinder, then your mass flow port does not impart much swirl into the cylinder but it flows a lot of air,” he says. “If you port out the swirl port and lose that rotational offed on the air it affects the air density distribution in the cylinder. You have the injector in the centre of the cylinder, and it directs the fuel particles out into the piston cup and ultimately into the full diameter of the bore. When you rotate the air in the cylinder you centrifuge the air out within the cylinder, so you are stacking up the air molecules around the perimeter of the cylinder wall, increasing the air density, then injecting into that density.
If you kill the swirl, you dont have that stratification of density, Imagine that each droplet of fuel burns as if you are peeling an onion – you are burning layers of molecules off the surface, it doesnt vaporise. The fuel particles need to be moving through the cylinder, and as they move towards the outside of the cylinder they need oxygen to keep combusting. With no swirl to increase the perimeter air density, you run out of oxygen. Once that happens, you are just turning the fuel droplet into a small piece of charcoal as it undergoes a reducing reaction, which then just gets blown out of the exhaust into the atmosphere. I am sure there is a passage in the Bible that says, ‘If you inject the fuel into the engine, you must use it there!”
With these observations in mind, in order to produce maximum power from a diesel engine and fully use the ability to run to high rpm, the right balance has to be struck between ultimate mass flow and retaining good inlet charge swirl. “You find a balance where you are getting as close to 100% combustion in the cylinder as possible, while maximizing flow,” Banks says.
Pistons
As already mentioned, engines such as the Duramax do not have a conventional combustion chamber, instead the bowl-shaped piston crown forms the chamber as it travels up the bore. The shape of the crown has a major impact on the way the air in the chamber moves, and this is an important design consideration. Once again, Banks highlights the importance of swirl and how modifications made to improve mass flow can be detrimental to this effect, reducing combustion efficiency.
With the pistons, the specific issues for swirl relate to the cutting of valve reliefs in the piston crown, which are needed to accommodate higher valve lifts. The shape of a diesel piston is very different from that of one from a spark ignition engine, and has a large bowl with a conical projection in the centre. This shape reduces the effective size of the combustion chamber as the piston nears TDC, and increases the velocity of the swirling mixture in the chamber.
“As soon as you put valve reliefs in the piston crown, it is like putting the brakes on air swirl – the reliefs provide more resistance to the swirling air, Banks says.So once again you have a balancing act: if you lose swirl then combustion is not as good, but if you don’t put reliefs in you cant run enough valve lift to get the airflow you need. You have no choice but to lift the valves more if you want to move air at high rpm, but with valve lift approaching 14 mm, we try to minimise the amount we need by finessing the balance of lift against the valve pocket design. lt takes a lot of time on the flow bench.
As well as ensuring that the piston crown is optimized for combustion, close attention must also be paid to the structural integrity of the piston and, most important, to ensuring correct cooling of the piston. “With the piston, you have a combustion cup sat just behind the ring pack, and you have to get the heat out of there. If you are only going to run the engine for a short duration then solid pistons can be used, but if you are going to run the engines for any length of time you are going to need a cooling oil gallery between the back side of the ring lands and the combustion cup,” notes Banks. Such a cooling gallery is very hard to incorporate with a forged piston, so Banks has tended to run many of his engines with cast-aluminium gallery-cooled pistons, which is not his preferred choice. Even when using thermal barrier coatings on the piston crown to reduce heat transfer, he still feels they are only good for short-duration running in the highest output applications.
One solution is to use a steel piston, which Banks developed with Mahle for a previous application and is looking to use with his Duramax engines. We developed those for a Cummins Marine application, and the forging dies were funded for that development, he says. Crucial to the piston cooling is the set-up of the piston oil cooling jets, which feed oil to the piston from its underside via a tapping to the main oil gallery. They extend all the way into the base of the piston at BDC, pushing through a spring steel flap to feed oil to the cooling passageway.
With the Cummins engine we developed the steel pistons for, we had to completely redesign the oil jets,” Banks says. “For that we used a two-stage external oil pump, with one stage providing the oil to the engine and the second just feeding the piston cooling. We were running in excess of 2 gallons per minute per piston, which is a lot of oil flow.” He notes that this was for a marine application, and that for a drag or road race engine, a lower flow could be used as the engine has a more varied duty cycle and the piston has time to cool.
Valve gear
The final pan of the jigsaw for making a high-revving, big-horsepower Duramax is the valve gear, says Banks. The standard Duramax parts are designed to last the lifetime of a truck and, as such, are massively over-built and thus very heavy. While the strength of these parts can be a benefit in some areas, it is definitely a hindrance in others. The first port of call for Banks was therefore to develop a lighter lifter (this being a pushrod engine).
“The roller tappets that come with these engines weigh as much as a Small Block Chevy piston. They are massive and are designed to go 500,000 miles – in fact l’ve seen a Duramax at 980,000 miles and it still made the same torque as when it left the factory. But some of the massive stuff has to go for high-rpm operation, so what we do is bush the lifter bores down to a size that will accept a Pro-Stock Chevy lifter diameter, and run that type of lifter. That means that, with the right springing, the lifters would be good for more than 10,000 rpm if need be,” says Banks.
The valve springs are also changed for a single, conical spring with a much smaller retainer than stock to reduce valve mass; for its drag race engines, Banks will even run a titanium retainer. The pushrod diameter is also increased. Interestingly the stock rocker arms have proved more than up to the task of controlling the valve. “So far, we have not had any issues with those, some people will knee-jerk replace everything, but I am the kind of guy who thinks if it isn’t broke, why fix it? We are however building a Spintron assembly at the moment to have a closer look at what the valves are doing. But so far we have not had any problems.
Conclusion
Although the market for high-performance diesel is only a fraction of that for gasoline race engines, the work that tuners such as Banks are doing is pushing that performance to record levels, which can be judged by looking at the Banks land speed record pick-up truck discussed in the sidebar, which is capable of running over 220 mph yet also returning better than 20 mpg at highway speeds. With a long-term government supply contract now sealed (also discussed in the sidebar), it will be interesting to see what further advances come out of Banks Power’s racing operations as it finds the time to develop the host of new ideas already brewing.
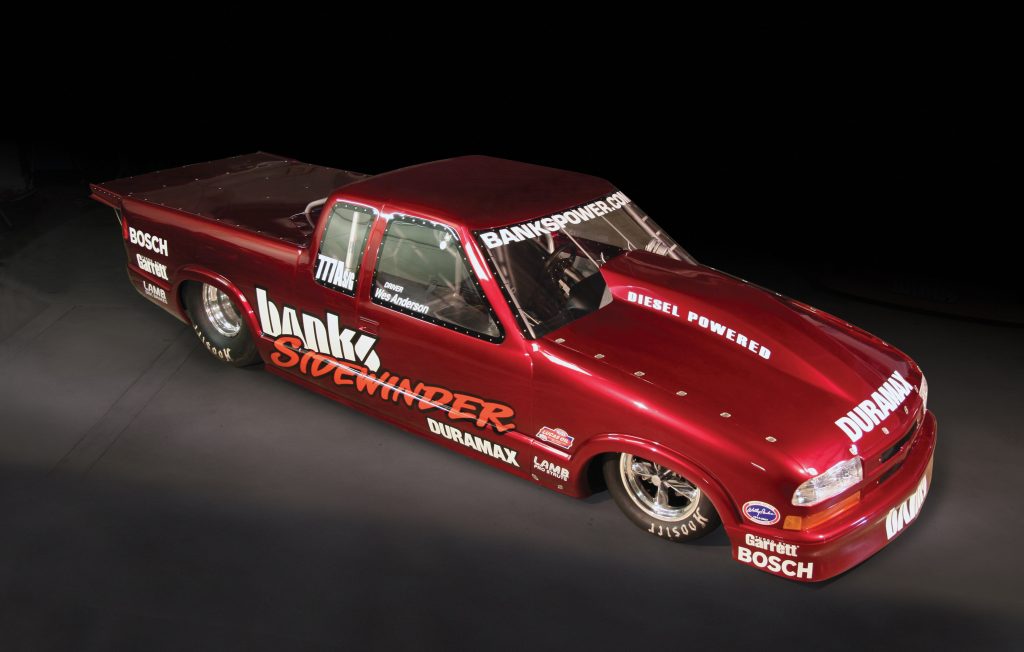
Gale Banks and Diesel
Banks did not start out in the racing world as a diesel fan, but his expertise in turbocharging led to an approach from GM in 1978 to work on the diesel engine it was developing for its 1982 model pick-up trucks. lt was a 6.2 litre V8, and GM wanted us to do a twin-turbo version for possible marine applications, he recalls. We had not done a lot of diesel up until then, in fact we had not even thought about it, but by 1982 we had developed a turbo system for the engine, before it was even released. That turbo system, I would argue, was the genesis of the turbodiesel aftermarket in the US. We still manufacture that product today.
Banks followed with an ’83 Ford kit and much more, but this development did not mark the start of a performance tuning bonanza for diesel in the US. Racing and the speed shops were not ready for diesel back in the 1980s, so it was probably at least 15 years until people caught on to it,” Banks says. Still, this early project for GM set the tone for Banks engine building over the next 30 years, and his company became synonymous with both racing and OEM high performance diesel engines.
To date, Banks has a host of racing records to his name in the arena of diesel competition. He has held the land speed record for a pick-up truck since 2002, which stands at a two-way speed of 21 7 mph, with his 5.9 litre, Cummins six-cylinder powered Dodge Dakota. He has also held the NHRDA Pro Stock diesel drag truck record first set in 2007 then raised to 7.77 s at 180 mph in 2009, it stood until late 201 3, and was set with a Duramax-powered Chevrolet s10.
In recent years, Banks’ attention has been distracted to an extent by a long-running development project to supply the engines for the US Armys Humvee replacement, The Oshkosh JLW (Joint Light Tactical Vehicle) is powered by the Banks 866T turbodiesel engine, which is based on GM Duramax architecture. However, at heart he still a racer, and now that the contract is finalized – a major coup for the company – he is keen to move forward with various racing projects that have been on the back burner for some time. One such project is to develop a dragster engine fitted with turbochargers as well as a crank-driven supercharger. Banks has already produced a number of these compounded engines for marine applications and racer Mike Ryans Pikes Peak Semi truck, which Banks was heavily involved in. The super-turbo diesel [as Banks refers to it] is something we are going to bring into the racing world, he says. Basically we ran the supercharger into the turbochargers on the Pikes Peak 14 litre truck, but I am also doing a V8 version where we are blowing the supercharger with the turbos, on my Top Dragster which runs in NHRA Sportsman, and we are going to try it with a Roots and a screw-type blower. “I want to find out if I can remove some of the supercharger parasitic losses at the crank using the turbochargers to unload the crank a bit by pushing the blower. This super-turbo thing is much like when we started out with turbocharging in the 1960s – there is no book on the subject. But it’s a lot of fun finding out,” he says.