Understanding Today’s Diesel
An in-depth look at how the modern diesel compares to gasoline engines.
Banks Project Sidewinder |
If you think diesel engines are noisy, smoky, slow and sluggish, then you probably think television sets have small oval screens, black-and-white pictures, and one tinny little speaker. Don’t despair. Many people have this perception of diesel engines, but friend, diesels have changed. Today’s diesels are not only powerful, economical, quiet, and environmentally clean, they are responsive and capable of performance that exceeds that of gasoline engines in many instances. Today’s diesels are different from those of just a year or so ago, and further evolution is just around the corner. For example, the world’s fastest pickup truck (222 MPH) is powered by an ’03 Cummins diesel, and this same pickup is quiet, street-driven, and even pulled its own support trailer to the Bonneville Salt Flats for the certified Land Speed Record runs (see Project Sidewinder Goes to the Salt elsewhere on this site)! And did we mention it made 1300 lb.-ft. of torque without leaving a trail of smoke?
What has been responsible for this dramatic evolution and refinement of diesel engines? The answer is the same thing that has given us full color, high-definition televisions with large flat-panel screens, digital picture and stereo surround sound quality: electronics. However, before we get into the electronic fuel management advancements, let’s review some of the basic differences, and similarities, of diesel and gasoline engines. Let’s start with gasoline engines.
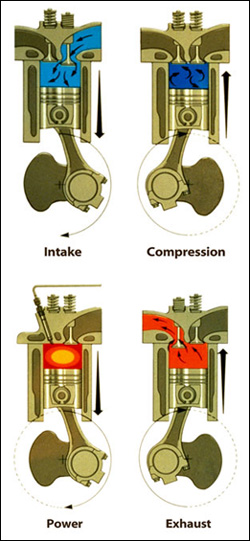
We will limit this review to four-cycle engines, commonly referred to as Otto-cycle engines after Nikolaus Otto, who patented this concept for engines in 1876. Most gearheads understand the basic operation of the gasoline four-cycle engine. The engine intakes air and fuel on the first cycle (downward stroke of the piston), it then compresses the air/fuel mixture on the second cycle (upward compression stroke). Ignition of the air/fuel mixture occurs when a spark is generated in the combustion chamber and the resulting expansion of the burning air/fuel mixture pushes the piston down to make power on the third cycle (downward power stroke of the piston). The following fourth cycle forces the spent exhaust gases from the cylinder (upward exhaust stroke). These four cycles correspond to mechanically-timed valve openings and closings to admit the intake mixture and permit exhaust flow. All of this is explained in detail in the accompanying article, “Airflow – the Secret to Making Power”. What is most significant about the gasoline four-cycle engine is how it is throttled, when the fuel is introduced, and how the fuel is ignited.
While gasoline engine operation is fairly common knowledge, some of the subtleties are not. A gasoline four-cycle engine is throttled by controlling the mass airflow into the engine. An air throttle regulates the density of the intake air admitted to the engine. Fuel is then added to the intake air in proportion to the mass airflow. This is done utilizing either a carburetor or a fuel injection system before the incoming air enters the cylinder. Consequently, it is a controlled density, proportionally mixed air/fuel mixture that enters the cylinder while the intake valve is open. After the intake valve closes, the thermal potential of the combustible mixture is set. No additional fuel can enter the cylinder, and the air/fuel ratio has been determined.
The air/fuel mixture is then ignited by a timed spark occurring as much as 50º to 60º of crankshaft rotation before the piston reaches top dead center (TDC) on the compression stroke, depending on engine speed, load, and throttle position. During normal power generation, ignition usually occurs later, and may occur as late as TDC. This allows time (in degrees of crankshaft rotation) for combustion to begin, generating peak cylinder pressure about 15º after TDC on the power stroke. Combustion may continue beyond this point, further assisting power generation, but the effective cylinder pressure drops due to the downward movement of the piston.
This rapid drop in cylinder pressure is dramatic. For example, let’s assume that the combustion space above the piston of given engine, with the crankshaft rotated to 15º after TDC is 6 cubic inches (about 82 cc). Let’s also assume the piston top has a surface area of 12 square inches, and that maximum cylinder pressure at 15º after TDC is 1000 PSI. This means there is 12,000 pounds of downward force on the piston. However, as soon as the piston moves just 1/2-inch farther down the cylinder, the combustion space will have doubled and the working pressure will have fallen to only 500 PSI, or only 6,000 pounds of force on the piston. Another inch of piston movement doubles the combustion space again, and the cylinder pressure will be only 250 PSI, or 3,000 pounds of force on the piston.
At this point, it should also be noted that burning time (in microseconds) for a given air/fuel ratio of gasoline and air at a given pressure remains fairly constant regardless of engine RPM. The air/fuel mixture burns, it doesn’t explode under normal operating conditions. If it does auto-ignite or explode, that’s uncontrolled combustion, which is called detonation. It is because of the burning time required for the mixture to generate heat and pressure that the spark timing must be advanced as RPM goes up. Burning time is required to heat and expand the gases (called the working fluid) in the combustion space to produce maximum cylinder pressure shortly after TDC.
Less often discussed are the pumping losses associated with four-cycle, air-throttled engines. Other than friction, pumping losses are anything that resists the rotation of the crankshaft. You might think of this as “negative torque” whereas anything that promotes rotation of the crankshaft is “positive torque”. Let’s consider this for each cycle.
On the intake cycle, a pumping loss occurs if there is anything impeding the free flow of air (and fuel) into the cylinder while the intake valve is open and the piston is descending. Other than the normal flow restrictions of the intake air ducting, air cleaner, intake manifold and cylinder head, the main obstruction of concern is the throttle if it is closed or partially closed. When this happens, the piston is trying to depressurize the cylinder and the entire intake conduit back through the intake port and the intake manifold against a flow restriction. More than anything else, it is this resistance to crankshaft rotation on the intake stroke that provides “engine braking” when the driver backs off the throttle. This is often erroneously called “compression braking”, but in truth, it has nothing to do with the compression stroke.
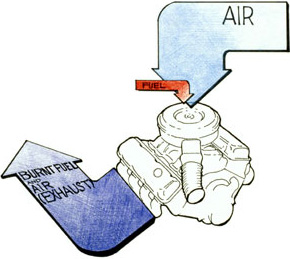
A good indication of the pumping loss on the intake cycle is manifold vacuum. The higher the manifold vacuum, the greater the pumping loss. It is worth noting that intake stroke pumping losses also occur at high RPM with a wide open throttle when the intake conduits can no longer pass all the air mass necessary to fill the cylinder to full atmospheric pressure at the end of the intake cycle. When this point is reached, both the volumetric efficiency and torque of the engine will begin to decline.
Also, factory compromises in the overall intake system can impose restrictions at all engine speeds. Gale Banks Engineering offers products for both gasoline and diesel engines aimed specifically at eliminating or reducing such restrictions to improve pumping efficiency and power output.
Interestingly, intake pumping losses can be completely eliminated at wide open throttle by supercharging (or turbocharging) an engine. Under such conditions, positive pressure (above atmospheric pressure) actually helps push the piston down on the intake stroke, adding torque. Of course, there is no “free lunch” and power to drive the compressor (supercharger or turbocharger) has to come from somewhere. For a supercharger, that power (or negative torque) comes off the crankshaft as it drives the supercharger. For a turbocharger, the negative torque comes in the form of an exhaust restriction that increases the pumping losses on the exhaust cycle. More on that later.
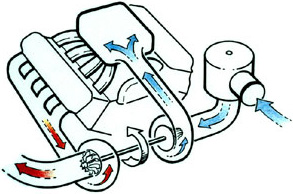
The compression cycle also offers resistance to crankshaft rotation as the piston tries to move upward compressing the air/fuel mixture. The greater the charge density in the cylinder on the compression stroke, the more force it will take to compress the air/fuel mass. In other words, on the compression cycle, the pumping loss is greatest at wide open throttle. Similarly, if the engine is supercharged (or turbocharged), the increased charge density will increase the pumping loss on this cycle. Regardless of throttle position or whether the engine is supercharged, the effective compression ratio of the engine also affects the pumping loss on the compression stroke. The higher the effective compression ratio, the greater the pumping loss. The good news is, no matter whether the pumping losses are high or low, these losses are mostly recovered on the power cycle. That’s why there isn’t any “compression braking”, as we’ll explain next.
The third cycle (power cycle) of the engine is the only cycle that does not have pumping losses. Even if there was no combustion of the air/fuel mixture, the piston would “rebound” downward from the compressed mixture with nearly the same force that it took to compress it on the compression cycle. This is why pumping losses on the compression cycle are not important. Yes, some of the work done on the compression cycle is converted to heat, and a small part of that heat is lost to the engine cooling system, but that is a very small percentage of the pumping loss that is not recovered. Of course, combustion does occur, but that simply adds to the downward force on the piston during the power cycle.
The fourth cycle (exhaust stroke) also requires effort to expel the exhaust gases from the cylinder. Because the hot, expanded exhaust gases still pressurize the cylinder to some extent, that pressure pushes against the piston as it rises. This cylinder pressure also promotes the flow of exhaust gases out of the cylinder with the exhaust valve open. The pumping losses on the exhaust cycle are directly related to the efficiency of the exhaust conduit. Anything that restricts exhaust flow, such as the turbine section of a turbocharger, or such as a restrictive exhaust system, increases the exhaust pumping losses. Here again, Banks offers products to reduce or eliminate factory exhaust restrictions and improve the efficiency of the exhaust system, thus reducing pumping losses and liberating power. In any case, the upward movement of the piston must displace any gases remaining in the swept volume of the cylinder, and that requires work.
Before going on to diesel engines, we should mention the pumping action of the underside of the pistons too. As a piston descends, it must displace the crankcase air under it. Similarly, when it rises it draws crankcase air behind it. At low speeds, the movement of air under the pistons balances out since on most multi-cylinder engines there are always as many pistons moving down as are moving up. At very high RPM, the crankcase air really doesn’t have time to move back and forth from cylinder to cylinder. Instead, it just compresses and expands under each piston, but again, expansion balances compression and there’s no pumping loss as a result. One of the benefits of a crankcase evacuation system that depressurizes the crankcase is that the density of the air beneath the pistons is reduced, further minimizing pumping actions.
Now let’s take a look at diesel engines. The most significant differences from spark ignition engines are that diesels have no air throttle, fuel is injected directly into the combustion chamber, diesel fuel is used instead of gasoline, and the heat generated by the compression of the air in the cylinders ignites the fuel when it is injected. Diesels also operate in a narrower RPM band than gasoline engines, and have lower peak RPM. This is because with direct fuel injection it is difficult to have good air/fuel mixture formation and full combustion over a broad RPM range. The higher compression ratio and cylinder pressure of diesel engines also requires heavier rotating and reciprocating components that limit maximum RPM. Few diesels operate at speeds above 4000 RPM, and most run notably slower than 4000 RPM. Diesels are thermally more efficient than gasoline engines because they operate at higher compression ratios than gasoline engines, and they have fewer pumping losses. Additionally, diesel fuel typically has about 11 percent more energy per gallon than gasoline. Typical diesel fuel has 138,700 BTU per gallon whereas typical gasoline has 124,800 BTU per gallon. Diesels can also run on much leaner air/fuel mixtures than gasoline engines, especially at idle. Let’s look at these things more closely.
Higher compression ratios result in more efficient burning of fuel in four-cycle engines. Most of today’s gasoline engines operate with static compression ratios between 8:1 to 10:1. Special high-octane gasoline permits slightly higher compression ratios (usually for racing), but the added cost and availability of high-octane (high lead) fuels precludes the use of higher compression ratios in most applications. Diesel engines, by comparison, operate at compression ratios between 14:1 and 24:1. Gasoline engines cannot operate at these higher compression ratios because the air and fuel is already mixed together before it enters the cylinder. At compression ratios above those usually used in gasoline engines, the heat of compression would cause the mixture to self-ignite too early, causing “engine knock”, parts damage, and a significant reduction in power. In a diesel, the air and fuel are handled separately. Only air goes into the cylinder on the intake stroke, and the pressurized fuel is injected after the air is compressed. During the compression stroke, the temperature of the intake air rises to as much as 1400º F. When injected into this hot environment, the fuel self-ignites. The injection of fuel is timed for minimal emissions, efficiency, and maximum torque generation. As with the spark timing in gasoline engines, the fuel injection timing is advanced slightly in some, but not all, diesel engines as the RPM rises. However, it should be noted that turbocharging quickens the burn time of the air and fuel as boost pressure rises. This means initiation of the fuel injection pulse must be retarded, or delayed, as boost pressure rises in a turbo diesel. In most diesels, the fuel injection timing changes for rising RPM and rising boost cancel each other out, and the timing of the beginning of the main fuel injection pulse remains relatively fixed. Depending on the design of the diesel engine, its intended usage, and emissions requirements, the fuel injection pulse can be set to begin as much as 24º – 26º before TDC, or it may be set to occur as late as TDC. In the Banks Sidewinder, for example, fuel is injected beginning 24º before TDC on the compression stroke.
Gasoline engines operate within a narrow air/fuel ratio range of approximately 12:1 to 15:1, although some modern “lean-burn” technology engines have been able to achieve significantly leaner air/fuel ratios.Diesels can operate with a broader range as rich as 15:1 or as lean as 60:1, however, going richer than about 22:1 to 25:l produces excessive temperature, soot, smoke, and poor fuel economy. Some aftermarket diesel chip manufactures simply dump in excessive fuel for power, causing the engine to operate in the undesirable rich range, as evidenced by plumes of black smoke. Thermal efficiency of diesels can be, and is, further enhanced with turbocharging to increase the available air (oxygen) to support combustion of more fuel. Gasoline engines cannot tolerate significantly higher cylinder pressure from turbocharging without creating preignition and/or detonation unless high-octane or ultra-high-octane gasoline is used.
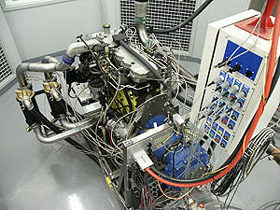
Diesel engines also have significantly lower pumping losses than do gasoline engines. Since diesel engine power output and engine speed are regulated by varying the air/fuel ratio through controlling the amount of fuel injected, there is no need for an air throttle. Consequently, there are only minimal pumping losses on the intake stroke. This also means that unfortunately there is virtually no engine braking when the driver backs off the fuel throttle pedal unless an exhaust brake, such as the Banks Brake is installed, but that’s a separate story. If the diesel is turbocharged, boost pressure can actually help generate “positive torque” on the intake stroke. Diesels do have high pumping losses on the compression stroke due to high compression ratios, but that is offset by nearly equal rebound on the power stroke, as explained earlier. Significant pumping losses occur only on the exhaust cycle, especially under boost conditions when a turbocharger is used, and such losses are more than offset by the added torque generated on the power stroke if the turbocharger is properly matched to the engine. The foregoing is assuming the exhaust conduits are sufficiently unrestricted for the size and power output of the diesel. If not, increasing the efficiency of the exhaust system will result in significant power gains. This is why products such as Banks Power Elbow, Monster Exhaust, Monster turbine outlet pipe, and Dynaflow mufflers work so well.
With all of the above taken into consideration, especially the lower pumping losses and greater thermal efficiency, it becomes clear why diesel engines are more efficient and produce notably more torque than similar displacement spark ignition engines. However, there’s more to the story. In describing the operation of the gasoline engine, it was noted that once the intake valve had closed, the thermal potential for that intake charge was set. The same is not true for diesel engines. The thermal potential for the power stroke in the diesel can be controlled by the amount of fuel injected and the length of time it is injected. The only limits to that are the amount of air in the cylinder to support combustion and the capacity of the fuel injection system. Because fuel can be injected longer into the power cycle to sustain effective cylinder pressure, torque output can be dramatically increased. This is largely responsible for the massive torque numbers diesels are able to produce. That’s explained in greater detail in another article on this site (see “Why Diesel Make So Much Torque” and “Racing the Diesel”).
Now that we’ve covered the basics of operation of the diesel as compared to the gasoline engine, we can discuss how electronic fuel management has contributed to the evolution of the modern diesel.
Until recently, diesel fuel injection was a purely mechanical function that varied the amount of fuel injected into the combustion chamber based on injection pressure that was controlled by fuel pump speed and the fuel throttle position that varied the fuel volume. Since the fuel pump was driven by the engine, pressure was a function of engine RPM up until a regulated pressure was reached. All of the fuel for the power cycle was injected in a single pulse. The fuel volume to be injected determined the length of the injection pulse. Some variation in the injection rate was possible, but it was minimal. This meant that combustion tended to be rich at the beginning of the burn and lean at the end of the burn. It also meant the engine produced a loud clattering sound at the beginning of combustion, less than ideal burn efficiency and notable soot in the exhaust.
Modern diesel technology utilizes significantly higher injection pressure. The transition to four valves per cylinder also allows positioning of the fuel injection nozzle directly in the center of the combustion chamber aimed into the middle of the cylinder. Further, computer-controlled fuel injectors can now be controlled to “shape” the fuel injection curve somewhat using multiple injection events during each firing cycle. This is possible by utilizing computer control of the injectors and ultra-high fuel pressure in a common fuel rail that feeds the injectors, hence the name “common rail injection”. This new technoloy allows controlling the air/fuel mixture for a more even burn with multiple injection events during the compression and power cycles. For example, a small amount of fuel is pre-injected early in the compression cycle to begin the burning process without the noisy clatter previously associated with diesels. Such a pre-injection pulse is called “pilot” injection. This is followed by the main fuel injection pulse dictated by throttle position. The timing and delivery of the main pulse also helps reduce combustion noise and emissions while producing optimum torque and fuel efficiency. And lastly, a post-injection pulse can help burn off soot produced during the main burn. This post burn occurs at a relatively low combustion temperature, and is sometimes referred to as a “cold burn”. Significant research continues in electronic fuel management to refine the injection process for reduced emissions and more efficiency.
Many positive things come from common-rail direct injection. First, power is increased up to 40 percent over older indirect injection designs while at the same time fuel consumption is up to 30 percent less. With less fuel consumption, carbon dioxide emissions are similarly reduced. These advantages occur largely because the higher injection pressure results in smaller fuel droplet size for faster and more complete combustion, and more even fuel distribution in the cylinder. For comparison, a modern common-rail fuel injection may operate at pressures as high as 19,000 to 24,000+ PSI, whereas the typical gasoline engine fuel injection system operates at only 40 to 60 PSI. Of course, the gasoline engines don’t inject directly into the cylinder, either.
Another significant difference between gasoline and diesel fuel has to do with the way the two fuels vaporize. First, it must be understood that liquid fuel does not burn. Only the vapor from the fuel actually reacts to oxidize, or combust. Gasoline readily vaporizes, and gasoline also has time to more fully vaporize after it enters the intake air stream and during the compression cycle before ignition occurs in a gasoline engine. Either any remaining liquid gasoline droplets in the cylinder vaporize during the combustion process or they are expelled unburned or only partially burned, on the exhaust cycle. Diesel fuel is another story.
Diesel fuel is less volatile than gasoline. It also enters the cylinder as a liquid, and combustion begins immediately. This means only the surface of the fuel droplets is vaporizing and burning, or stated more correctly, reacting with the oxygen around it. The heat of the combustion causes the next layer of the droplet to vaporize, and if the droplet finds available oxygen, it then reacts. This process continues like peeling away layers of an onion until the fuel droplet is fully consumed, or the droplet fails to find oxygen and the fire goes out. Technically, it is also possible for the droplet to collide with the piston top or cylinder wall, which typically terminates combustion. Considering this process, the smaller the diesel fuel droplets are when they exit the injector nozzle, and the faster they are traveling, the more likely the droplets are to find available oxygen and complete combustion before colliding with the piston or cylinder wall. This is one of the big reasons for the ultra-high common-rail injection pressure.
There is a negative associated with modern common-rail diesels. The more sophisticated fuel injection system is expensive to manufacture, now accounting for 30 to 40 percent of the cost of a modern diesel engine. Diesel engines still require more robust components to withstand the higher compression ratios, higher turbocharger boost pressure, higher cylinder pressure, and greater torque output than similar sized gasoline engines too. This results in diesel engines being heavier than similar displacement gasoline engines. However, progress is being made in these areas. Some diesels now use aluminum cylinder heads to reduce weight.
In comparison to gasoline engines, modern diesels produce 30- to 40-percent less carbon dioxide, very low hydrocarbon and carbon monoxide levels, and over their usable life, diesels produce less oxides of nitrogen than gasoline engines. Cooled exhaust gas recirculation (EGR) can help diesels further reduce oxides of nitrogen and soot formation, and some new diesels are EGR-equipped. Unfortunately, the application of cooled EGR does have a negative impact on efficiency and fuel economy. Significantly reducing the remaining oxides of nitrogen is feasible with catalytic converters when ultra-low-sulfur diesel fuel replaces existing diesel fuel, as mandated by the Environmental Protection Agency by 2006. The sulfur in current diesel fuel damages the oxides of nitrogen-reducing catalytic converters now available. The sulfur in today’s diesel fuel also contributes to the smell associated with diesels. When the sulfur goes, so will most of the diesel odor. The problem, if there is one, is that even today’s clean diesels still can produce some particulate matter in the form of smoke or soot. This is minimal compared to diesels of just a few years ago. In fact, the particulate levels are so low that the smoke is barely detectable with the naked eye, but some people perceive any smoke as unhealthful. Considerable debate continues regarding whether the current levels of diesel emissions reach a threshold that is harmful to humans.
With all of the gains made in today’s modern diesel engines, the future of diesel appears bright. The diesel engine is the most fuel-efficient energy-conversion device in mass production today. State-of-the-art diesels are setting performance records that eclipse gasoline engines. Having already overcome most of the objections against diesels, engineers continue to refine electronic fuel management and emission controls. Diesel fuel is more commonly available at many service stations, eliminating yet another perceived disadvantage. Meeting future emissions requirements might prove to be problematic, but not impossible. All that remains to be changed is the public perception of diesels.
You owe it to yourself to check out today’s new diesels. After all, you’re not still watching a black-and-white TV, are you?