Truth in Testing
Dynamometers and flowbenches are great diagnostic and testing tools. In essence, they are scales for measuring performance. Just be sure there’s not a thumb on the scale.
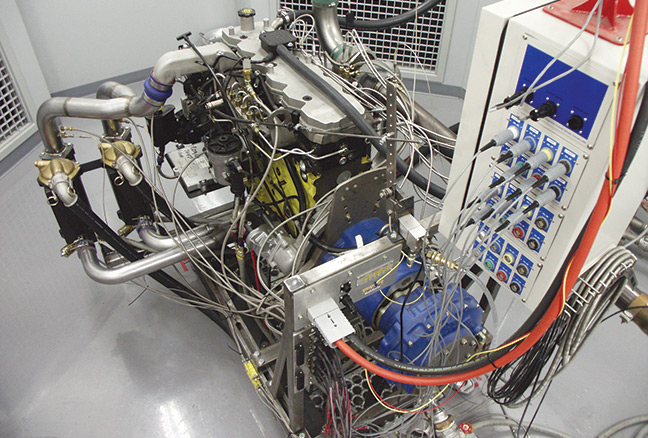
The term “dyno tested” is used a lot these days, and most people tend to accept dyno results as absolute truth. Unfortunately, dyno results are no better than the testing method used to get the results. In other words, unscrupulous operators can make the results come out to be almost anything they want. It all comes down to the testing method and the ethics of those doing the testing. Let’s look at a quick example. A vehicle can be placed on a chassis dyno and accelerated to speed. Let’s say this speed is 60 MPH. At this point the vehicle’s engine could be switched off and a dyno reading taken. It would show a power reading even though the engine is no longer running! Why? The inertia of the rollers and the spinning tires would provide a reading.
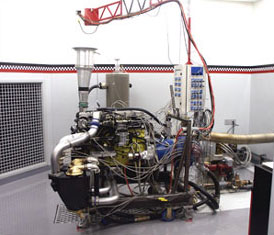
The above example might seem far-fetched, but in truth the inertia effect of any dyno, be it a chassis dyno or an engine dyno can contribute to a flash reading that is higher than what the test vehicle or test engine could sustain under an extended steady-state load. This is a very common method of “cheating” a dyno test. Of course, the results of such a test are meaningless, but the operator can say, “The dyno showed a reading of such-and-such.”
At Gale Banks Engineering, we’re sticklers for testing using proper scientific testing methods. That means testing under controlled and monitored conditions, elimination of outside variables, and sustainable results. Dedication to such testing begins with the test equipment. All Banks test fixtures have the capacity for sustained load operation. All test equipment is calibrated before testing begins, and every test is fully instrumented with the results correlated to standard conditions. It’s the only way to compare apples to apples – to get honest results to reveal if real progress is being made.
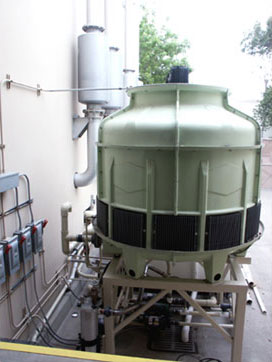
We have seen some dyno facilities that simply don’t replicate real world conditions. For example, an engine dyno cell may lack adequate climate control. In such cases, the cell gains temperature during testing, which in turn changes the intake air temperature (see “Cool Air Equals Power“). Worse still are dynos that don’t have adequate engine cooling water, and more importantly, adequate dyno water-cooling facilities. A water-brake engine dyno converts engine power into heat in the absorbing unit. If the water to the absorbing unit becomes progressively warmer, the water will not absorb as much heat as if it was cool. Hence, the dyno readings would change. At Banks, the dyno cells have high capacity environmental facilities and massive water tanks and heat exchangers for engine and dyno operation at a constant temperature. Similar heat problems occur on chassis dynos if the rollers and the vehicle tires get hot. It is essential to cool both with an adequate supply of cool air. It is also necessary to move air thru the vehicle’s radiator, and intercooler if so equipped, at a rate consistent with the roller speed to simulate actual road conditions. All of these things are done on Banks’ chassis dyno. Assuring consistent testing conditions is the responsibility of the dyno operator. It can also be a manipulation factor for an unethical dyno tester.
As important as temperature is to the test facility, it is even more important to the engine or vehicle being tested. Simply checking oil temperature and water temperature isn’t nearly enough. An engine needs to heat soak to the same level before each test. For example, if an engine is initially warmed up and then tested, and then allowed to sit for ten minutes before the next test, the block may have gained 30º F. due to heat soak. That change in temperature will change the internal dimensions and clearances of the engine. The second test cannot then be compared to the first test. The same thing applies to the tires and rollers on a chassis dyno.
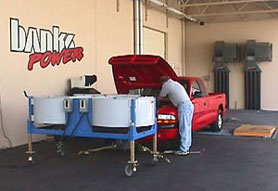
The same rigorous standards are applied to flowbench testing. The equipment is checked, temperature and relative humidity measured, and components are flowed under as realistic conditions as possible. What does that mean? Let’s consider flow testing a muffler. For realistic results, the muffler must be flowed with the appropriate exhaust pipe and tailpipe in place. Any comparison to other mufflers must be done with similar inlet and outlet pipes in place. Doing such tests any other way would be to “fudge” the results.
In conclusion, testing of any kind, be it on a dyno, a flowbench, or even a road test, the results are only as good as the testing method, and more importantly, the ethics of the tester. False or inflated claims, however, have a way a coming around to bite the ones who foster them on their unsuspecting customers. In the end, if the products don’t live up to claims that are made for them, the word gets around. At Banks, we’re proud of our reputation. We test more than anybody else in the industry to be sure our products are the best. That’s the way it’s always been. That’s the way it will always be.