Header Flanges
(From the Archives – 04.05.02)
You might think that discussing header flanges is about as exciting as listening to a lengthy dissertation on muffler bearings. In most cases, you’d be right. But when I toured the tube shop here at Banks, the first thing that got my attention were the header flanges. They’re the thickest and flattest I’ve ever seen. There are several reasons for this.
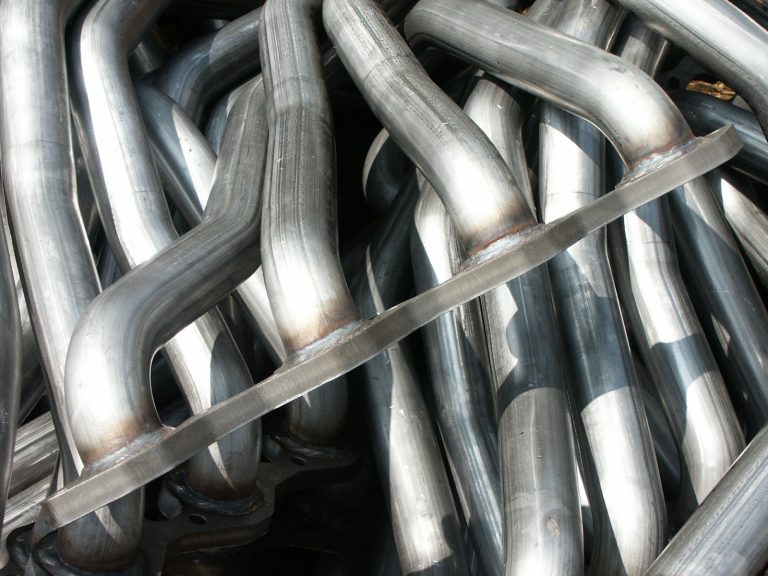
If you build turbocharged racing engines, you learn about exhaust flanges in a hurry. Gale not only built turbocharged racing engines, but he built them for endurance racing boats. This puts more load and strain on an engine than any other type of racing I can think of, with Bonneville coming in second—another activity with which Gale has plenty of experience. Turbos build extreme heat and pressure in the exhaust system, especially in a sustained racing application. This can quickly lead to warping or cracking of header flanges or tubes. If such warping or cracking leads to exhaust leakage, the turbo will lose boost and the engine will lose power—not what you want during a race. Regular tube headers will not hold up with a turbo in a high-performance application. In most of his set-ups, especially the twin-turbo configuration, where the turbo mounts on the manifold, Gale uses his own cast iron exhaust manifolds. In the few instances where I’ve seen him build tubular headers for twin turbos, he used super-thick flanges and tubes fabricated from forged stainless steel bends. Before I saw them, I didn’t know there was such a thing as forged stainless steel tubing.
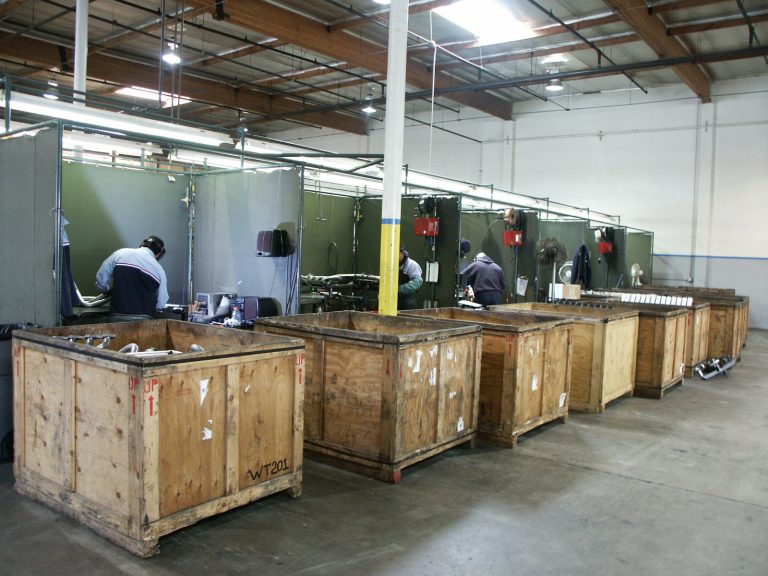
As I have mentioned before, we don’t use the term “headers” here at Banks. We call them TorqueTubes, a registered Banks trademark. Personally, I think of torque tubes as enclosed driveshafts. I have two of them, one in my ’48 Chevy and one in my ’32 Ford. I’m antiquated. But I’m getting off the subject.
At Banks today, we retain cast iron exhaust manifolds for all turbocharged diesel applications. But for all gasoline applications, at the PowerPack level, we supply TorqueTube exhaust manifolds. More than the name differentiates them from other headers.
In heavy-duty truck towing, and especially in a motorhome environment, where the engine is not only pulling a heavy load, but is enclosed in a box, the exhaust manifolds suffer the same sort of punishment doled out by turbochargers—extreme heat and exhaust gas pressures. As described by longtime Banks employee Bob Robe, even the cast-iron exhaust manifolds on big block GM engines in motorhomes can take on the appearance of a “miniaturized El Mirage dry lake surface” because of cracking, and can actually swell and bulge from exhaust pressure. Big block (460) Fords are known for breaking exhaust manifold bolts in similar situations.
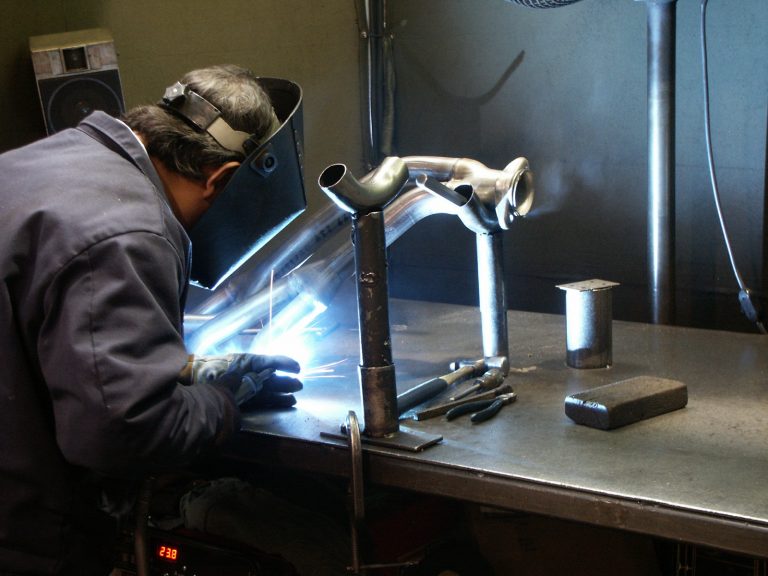
So Gale Banks applied his turbocharger experience when designing his TorqueTube exhaust manifolds for trucks and motorhomes. It starts with the flanges. They are all 5/8-inch thick. That’s more than half an inch. Nobody else makes headers with 5/8-inch thick flanges. Most are in the 1/4 to 3/8-inch thick range. Headers with 5/8-inch thick flanges aren’t going to warp or crack under any earth-bound conditions.
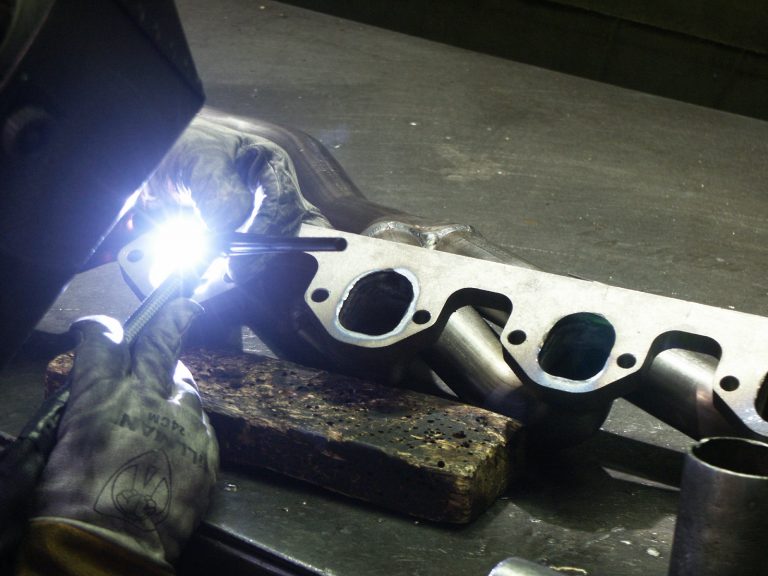
Second, Banks TorqueTubes are double welded at the flanges. After the flange and individual tubes are assembled in a jig—what tube shop manager Ralph Bolam calls “positive point fixturing” (and there is a positive point fixture for everything made in the shop)—and tack-welded in place, then they are TIG welded around the inside diameter of each tube in the flange. After that, they are MIG welded around the outside diameter of each tube at the flange. Nobody else does this. Most regular headers are made by pushing the tubes slightly through the flange, MIG welding them to the flange on the side that mates to the head, and then grinding the welds to make a flat surface to mate with the exhaust gaskets and the port surfaces of the head.
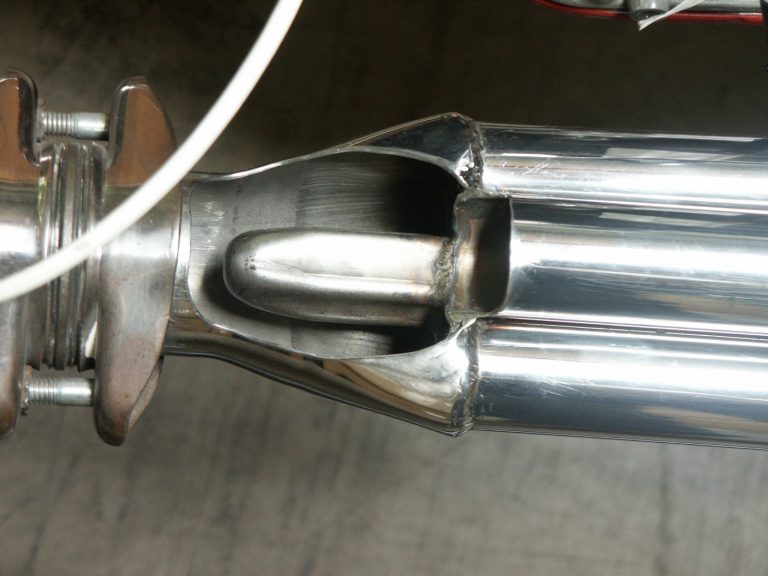
What are MIG and TIG welding? MIG stands for metal inert gas and is commonly known as wire welding. It has generally replaced arc welding—or stick welding—as a fast and clean type of production welding. When the welder pulls the trigger on the torch, or “gun,” it emits a metal wire that is fed from a spool in the welder, and it also feeds a mixture of inert gases around it. The wire can be any of various kinds of metal (depending on what metal is being welded), and it acts as both electrode to create a spark, and as filler material at the same time. Both the speed at which the wire is fed and the voltage of the spark are controlled by knobs on the welder to adjust for the thickness of metal being welded. The inert gas acts as a shroud around the spark to reduce spatter. The standard gas for MIG welding is 75% argon/25% carbon dioxide, and you get it in a bottle or tank, with a regulator, such as for gas welding. However, at Banks we get gas by the truckload, and Ralph, through experimentation, has come up with his own special mix that he will not divulge. But it obviously works very well, as you can see in the photos.
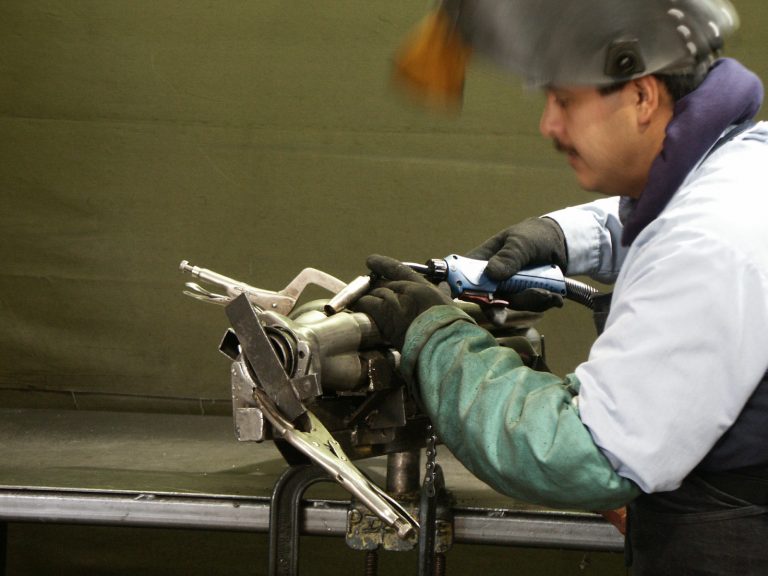
TIG welding, which stands for tungsten inert gas, is generally considered superior to any other type of production welding. To do it well is an art. It also uses a shroud, or cloud, of inert gas to isolate the weld—usually straight argon—but in this case the electrode is a pointed metal rod—usually tungsten (hence the name)—which does not actually touch the metal being welded. A foot pedal controls the voltage, or intensity, of the weld, and usually thin welding rod is used as a filler, as in gas welding. When done properly, TIG welding (also known as Heli-arc because helium was initially used as the inert gas) produces a very thin, even bead with no spatter, but with very good penetration. Because it takes so much longer to do, it is usually only used when superior looks or strength are required.
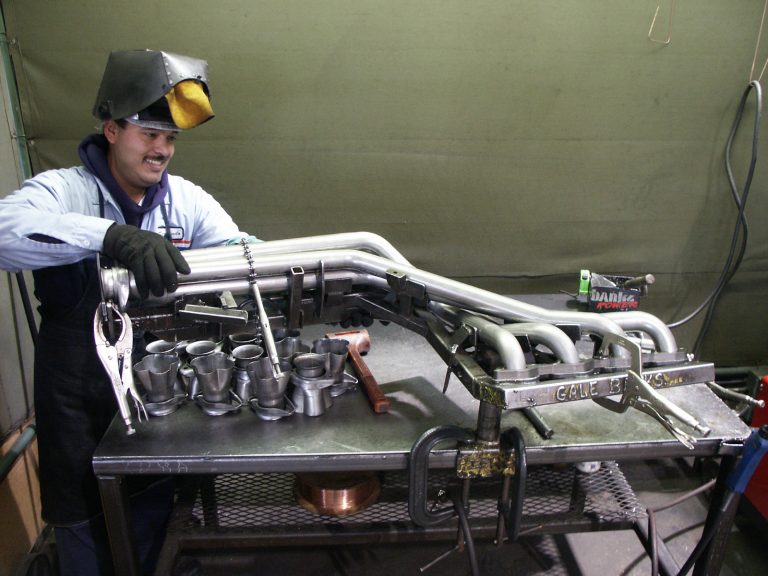
While the flanges themselves are made of A-36 mild steel plate, which are laser cut to shape out of house (we go through 800 to 1000 flanges a month here), the actual tubes of Banks TorqueTubes are all made of 409 series stainless steel that is mandrel-bent to shape in the tube shop. This, again, is highly superior to most headers.
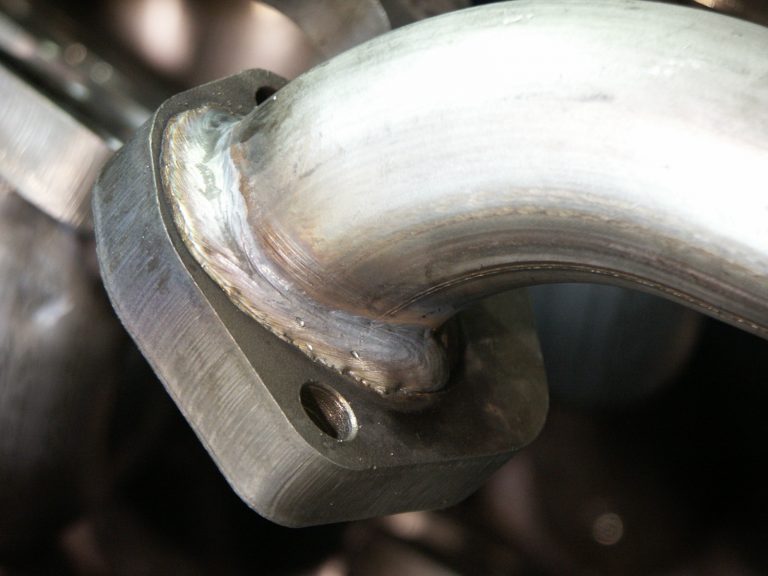
But the most amazing step in the construction of a Banks TorqueTube is that each one is mounted in a huge mill (we have a horizontal one and a vertical one fixtured to do TorqueTubes) to have the face of the flange milled perfectly flat. This is unheard of. It is very time-consuming (each manifold takes 7 to 8 minutes to mount and machine on the horizontal mill; the vertical one goes faster). Any time metal is welded, it warps to some degree—even 5/8-inch flanges. So after all the welding is finished on each TorqueTube, the flange is machined flat, as the port surfaces on the cylinder head were at the factory, so the two can be bolted together with no gaskets or any other kind of sealer (on engines with aluminum heads we still use gaskets because of dissimilar expansion rates of the metals, but we probably don’t really need to). So, not only will Banks TorqueTubes not warp or crack in the severest motorhome setting because of their 5/8-inch thick flanges and stainless steel tubing, but they also have no gaskets to blow out. It’s commonly known as bullet proof.
Bet you never knew there was so much to know about header flanges. Now, about muffler bearings…
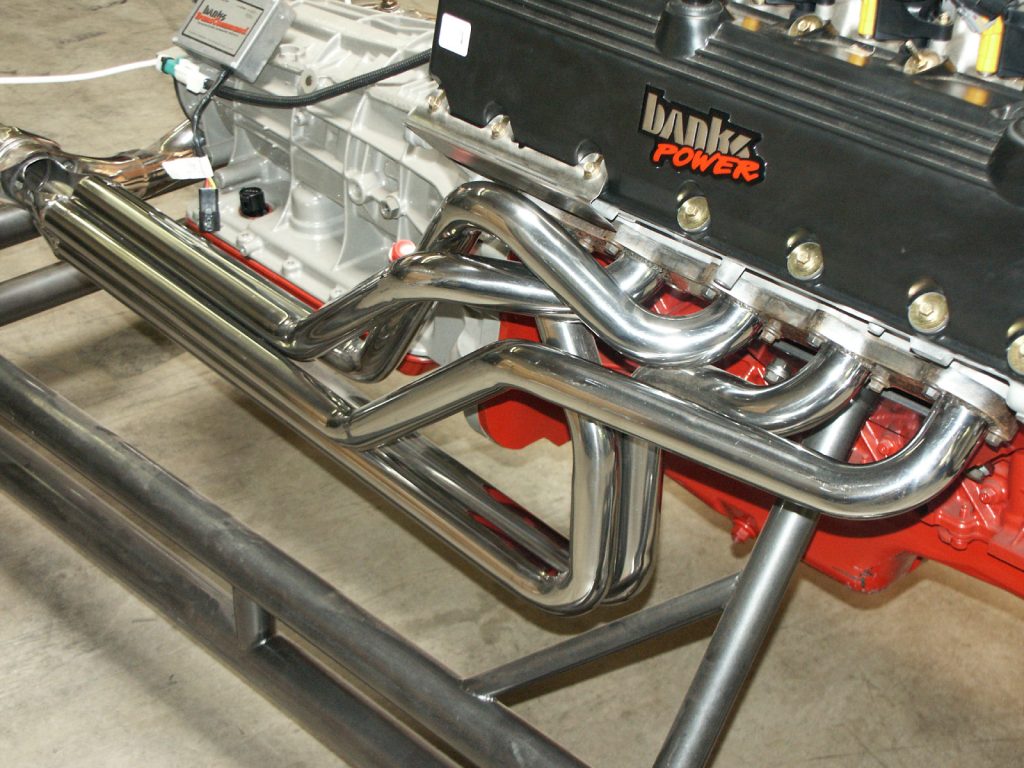
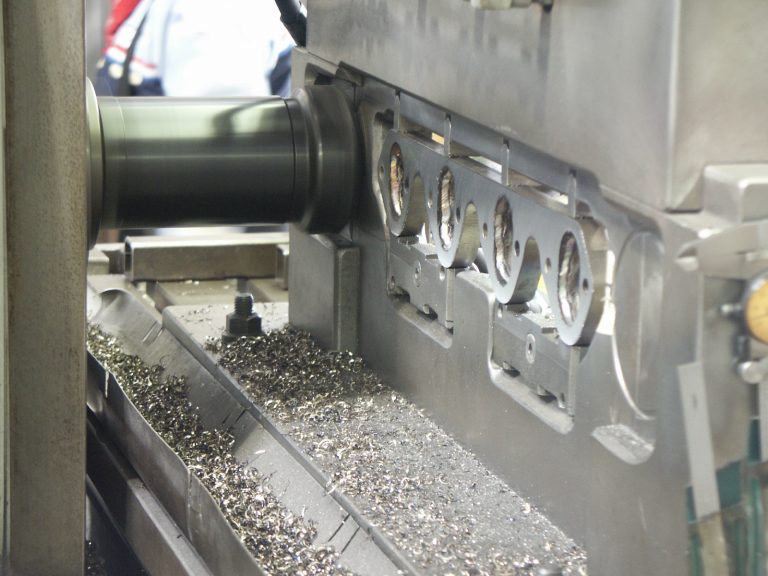