Basics of Manufacturing
Full Video Transcripts
00:00 there are two popular methods of casting
00:02 aluminum sand casting and diec casting
00:05 sand casting involves Molen metal being
00:08 poured into a sand mold the only thing
00:10 helping the aluminum to flow into the
00:13 mold is Gravity the sandcast mold is
00:16 rough and typically leaves a rough
00:18 finish another problem is paracity
00:21 that’s where voids or holes in the
00:23 casting are caused by hydrogen gas
00:26 entrapment when you sandcast thicker
00:29 walls are required to avoid cold shuts
00:32 cold shuts are where streams of metal
00:35 entering the mold through various Gates
00:38 don’t completely fuse together due to
00:40 premature cooling which brings me to
00:42 diec casting with diec casting aluminum
00:45 is a rammed into the Bold aluminum is
00:48 heated to,
00:49 1300° injected into a preheated h13 tool
00:54 steel mold at 5500 lb per square in it
00:58 happens instantaneously
01:00 the result is a Precision casting with
01:03 no paracity no cold shuts and no welds
01:07 the surface finish is as smooth as a
01:09 baby’s butt which is good for fluid flow
01:12 well I’ve got news for you this is the
01:15 new banks Ram Air transmission pan our
01:19. latest durability tool with the banks
01:21 Ram Air transmission pen for the Allison
01:24 56 and 10 speeed it’s the best at
01:26 lowering fluid temperatures
The new Banks Ram-Air Transmission Pans for the Allison 1000, Allison 10L1000 and Chrysler 68RFE are die cast, not sand cast. In his latest video, Gale Banks explains the basics of aluminum casting and why sand casting is a bad idea.
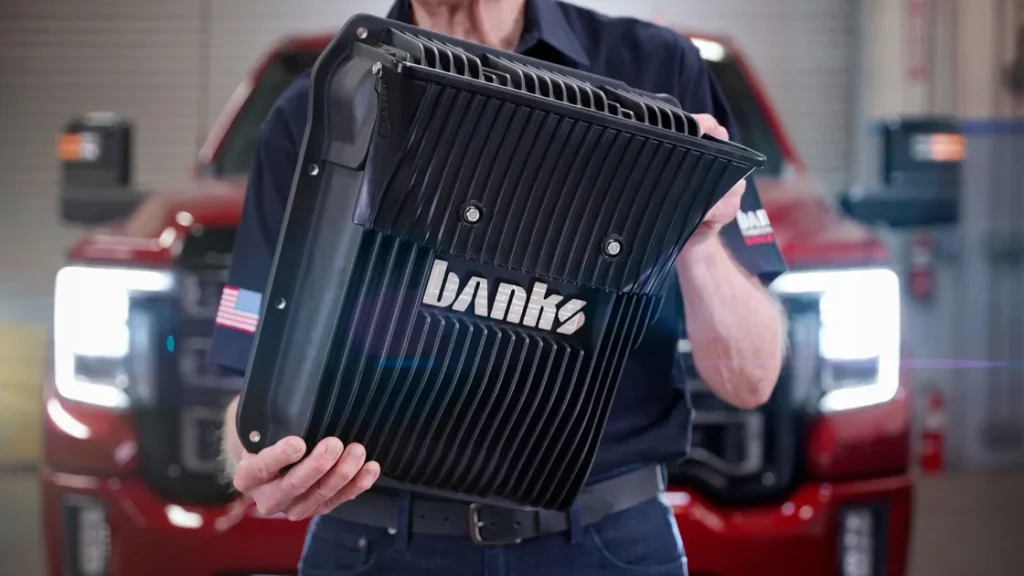
There are two popular methods of casting aluminum; sand casting and die casting. Sand casting is one of the earliest forms of metal casting. This primitive method involves molten metal being poured into a sand mold. The only thing helping the aluminum to flow into the mold is gravity. The sand mold is rough and typically leaves a rough finish. Another problem is “porosity.” That’s where voids or holes in the casting are caused by hydrogen gas entrapment. And, when you sand cast, thicker walls are required to avoid “cold shuts.” Cold shuts are where streams of metal entering the mold through various “gates” don’t completely fuse together due to premature cooling. That’s why some of these aftermarket pans are so thick. Often, if you look closely, you can find welds in the casting where a cold shut has been repaired (see video). We never sand cast our lubrication products. This eliminates any risk of sand contamination of the fluid.
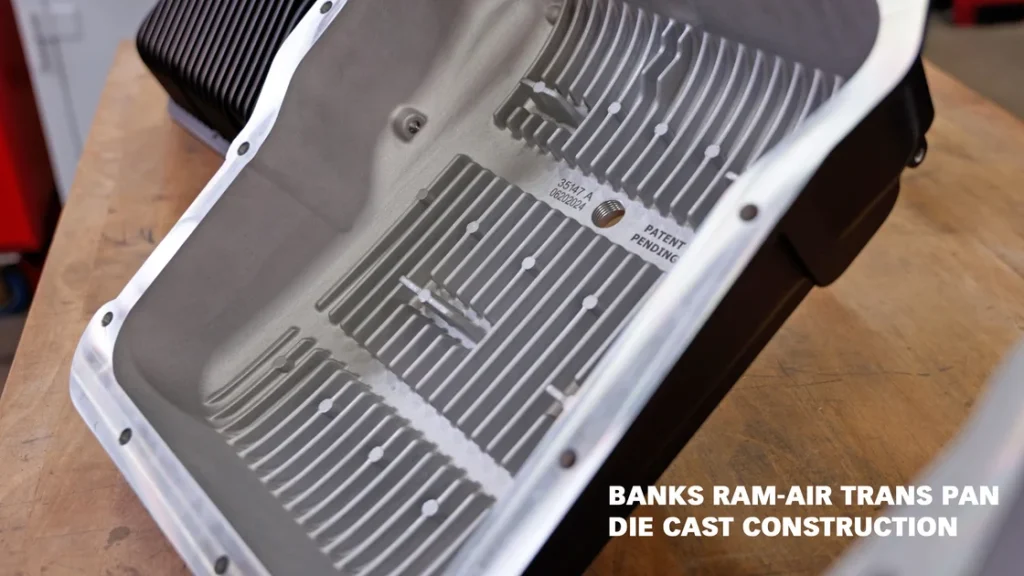
With sand casting, aluminum is poured into the mold. With die casting, aluminum is rammed into the mold. Aluminum is heated to 1,300° and injected into a preheated H13 tool steel mold at 5,500 PSI. The result is a precision casting with no porosity, no cold shuts, and no welds. The surface finish is as smooth as a baby’s butt, which is good for fluid flow. And, the walls will be thinner and dense, which is great for heat transfer and thermal recovery. In other words, thinner, denser walls allow heat to exit more quickly. The only downside to die casting is that the molds cost a fortune, but the result is worth the effort.